How To Perform a Professional Brake Job (Have video below)
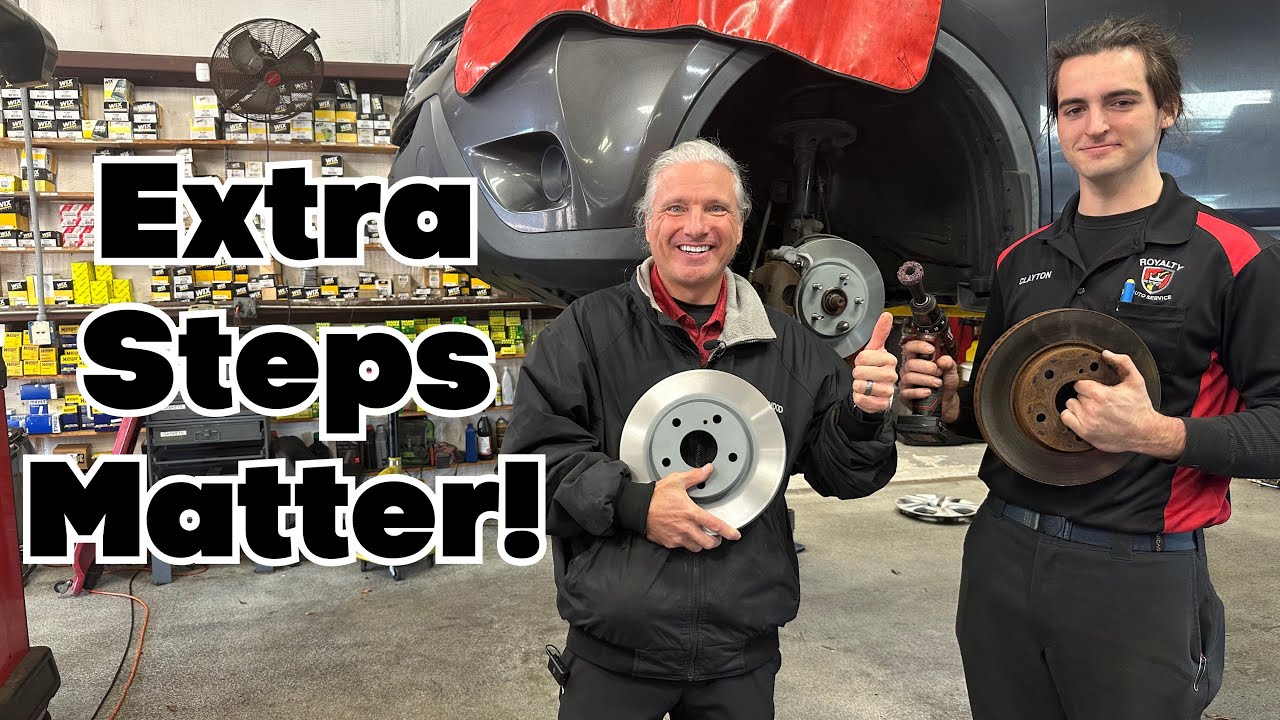
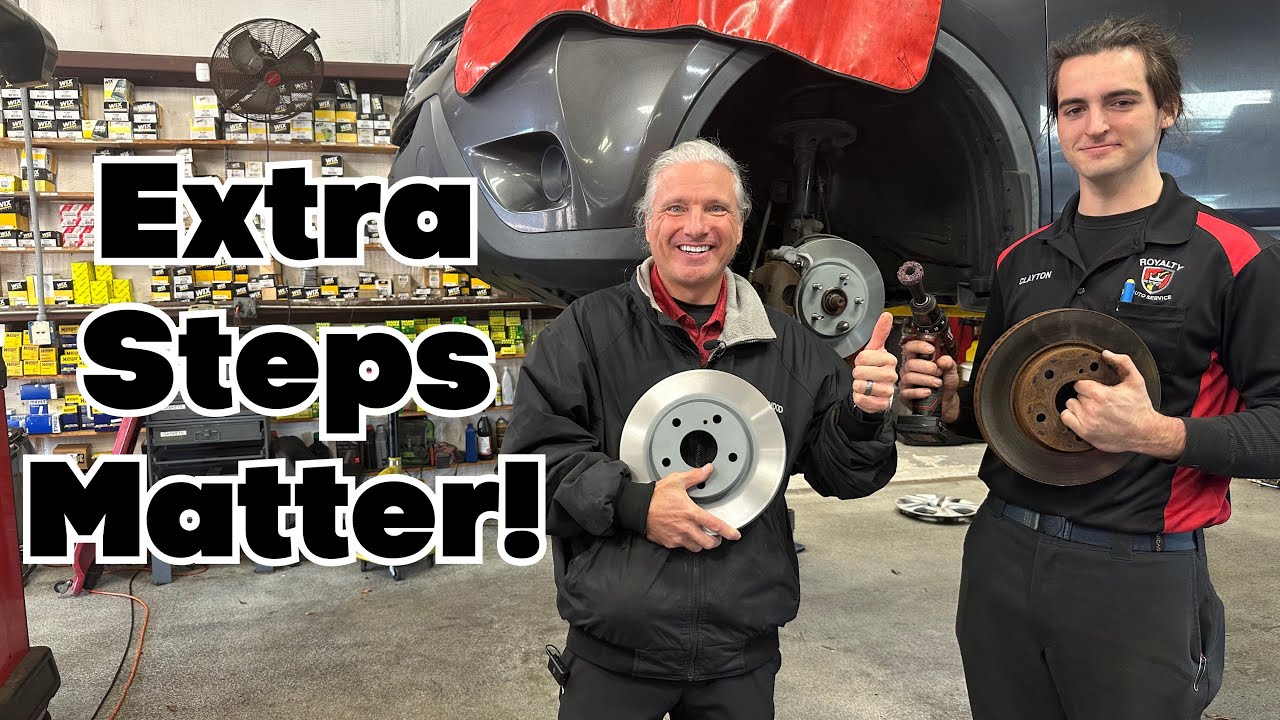
How to Perform a Professional Brake Job (Pads & Rotors)
Today, we have a Toyota in the shop for a brake job, and we’re using this opportunity to walk you through the correct and professional way to do it. Our method ensures minimal brake comebacks, eliminating issues like vibrations and noise complaints. While there are quicker ways to do this, we believe in doing it the right way for the best long-term results.
Step 1: Removing the Brake Components Properly
Clayton, our technician, is starting by carefully removing the brake components. One crucial step is never hanging the caliper by the brake hose, as this can compromise the hose and lead to failure. Instead, we use a proper caliper hook to keep the hose protected.
Step 2: Cleaning the Hub Surface
Once the rotor is removed, the hub surface must be cleaned thoroughly. Even minor debris can cause runout, leading to vibrations and uneven wear. A properly cleaned hub ensures the rotor sits flush, preventing unnecessary warranty work in the future. For heavily corroded hubs, we use specialized cleaning tools, but a wire brush can also get the job done.
Step 3: Cleaning and Lubricating the Caliper Bracket
The caliper bracket is another critical component that must be cleaned. Rust and dirt buildup in the guide areas can prevent the brake pads from moving freely, leading to uneven wear and braking issues. We remove old hardware, clean the contact surfaces, and install new anti-rattle clips to ensure smooth pad movement.
Step 4: Inspecting and Lubricating the Slide Pins
Slide pins must be inspected and cleaned before reinstallation. If they stick, the caliper won’t apply even pressure, causing premature pad wear. We use high-temperature brake grease, ensuring they move freely but without excessive lubrication that could attract dirt. Never use white lithium grease or wheel-bearing grease, as they are not designed for high brake temperatures.
Step 5: Compressing the Brake Caliper the Right Way
When compressing the caliper piston, we always open the brake bleeder valve to prevent dirty fluid from being pushed back into the ABS system or master cylinder. This prevents contamination and potential damage to expensive brake components.
Step 6: Installing the New Brake Pads & Rotor
Before installing the new rotor, we ensure that any protective coatings remain intact, as they help with pad bedding. The rotor is secured, and the new brake pads are installed by hand—never forced in. We apply a small amount of brake lubricant to the back of the pads where they contact the caliper to reduce noise and vibration.
Step 7: Torquing Bolts & Final Checks
We tighten all bolts to manufacturer-recommended torque specs. This ensures proper clamping force and prevents over-tightening, which could lead to component failure. Before finishing, we pump the brake pedal to restore pressure and bleed the brakes if necessary.
Conclusion
This method takes slightly longer, but it ensures quality, longevity, and customer satisfaction. Taking the extra time to clean, lubricate, and properly torque components prevents comebacks, noise, and uneven wear. A well-done brake job saves time and money in the long run, ensuring safe and smooth braking performance.